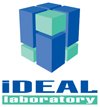
Super User
Arcu laoreet eget Vestibulum quis fringilla hac ut consequat pellentesque tellus. Lobortis nunc sed laoreet vitae Cras parturient dui nibh wisi interdum.
About us
Ideal Laboratory was born in 1991 created by Celestino Donati and Marco Baglioni and started to work at high levels ever since.
In years has become one of the main laboratories in italy thanks also to many conferences and awards to one of its owners, Celestino Donati.
The professional growth brought Ideal Laboratory to expand its members and in 2001 the laboratory got 2 more owners -Tommaso Minelli and Fabio Verzulli – with the right skills to raise the level of the company.
Today Ideal Laboratory has 16 operative work locations divided by sections, spreaded in more than 250 squared metres split in 2 floors; esthetic section, temporaries section, bite plane section, denture's section, plaster room, frame's section and CAD/CAM section.
The strategy of the laboratory has 2 receptionists, an amministrative department, and an organisation of delivery/withdrawal dedicated and dislocated around Rome and most parts of Italy.
All the materials and machines have been chosen in order to get the maximum esthetic and functional result so the laboratory has become one of the main laboratories for many materials, implant system and machine's production companies in italy. The laboratory owns the first CAD/CAM system delivered in Italy (Noritake) as well as the CAD/CAM Yena with Dental Wings software and a Nobel Procera. Reminding that Ideal Laboratory has all these machines at their latest version and update.
The presence of all these different machines allows the realisation of high quality and esthetic prothesis on any implant platform, and makes possible the realisation of prothesis in Zirconia, Allumina, Disilicate, Titanium, Monolites, and Cr/Co, either is a crown, a bridge, an abutment, an implant bridge or full arch restorations, in different timing and ways according to the dentist's needs.
With the acquisition of the Dream Frame technology, since 2013 Ideal Laboratory is realising frameworks in Carbon Fiber highly biocompatible, resistant, light and able to relieve the masticatory forces either in compression and in flexion.
There are no beginners in Ideal Laboratory, and there's no turn-over: the dental technicians raised here stayed here all along, and became excellent professionists.
Ideal Laboratory executes its jobs EXCLUSIVELY on SAM articulators and UNDER MICROSCOPE.
Careful to the evolution of the sector and for years operative in prothesis on guided implant surgery-after the brilliant results obtained we are considered the landmark in implant prothesis – we always pay attentions to the new developments and to the consequent investiments, also in terms of softwares and hardwares.
Every machine (for example the disposal of 6 Zeiss and Leica microscopes) is only used for a precise step, and not for multiple use, from one side this brought the company to a bigger and more expensive investment but on the other hand every machine is selectioned for a specified use costantly under control.
Ideal Laboratory is subjected to quality control and ISO 9000: 2001 since 2005 by the Certification IMQ.
Tommaso Minelli
General Manager / Owner
He is the technologic person of the laboratory.
Since his first years has put his attention to metals deepening on their merceologic and physic characteristics and their application.
He is involved in precision techniques and follow the development of the new dental technologies.
He has participated to many master courses such as the master metal course at the Argen Headquarters in San Diego, CA. and an implantology course at the Chieti University.
Specialised in the realisation of frames and abutments in every material (Carbon, Zirconia, Cr/Co, Gold and Titanium) with CAD/CAM technology (Exocad, 3Shape, Dental Wings, Nobel Procera) and other techniques.
Celestino Donati
General Manager / Owner
He is involved in esthetic from the single unit to the full arch jobs.
Is the author of many articles and conferences on esthetic, precision and gnatology.
In years he's become a reference person in Europe for Esthetic Designs.
He has participated to master courses on esthetic in Japan at the Kuwata College.
He collaborates with the Dentistry section of the Tor Vergata University in Rome for the realisation of prosthetic works.
Plaster
A space of more than 30 squared meters subject to umidity percentuage control (to keep the merceologic characteristics of the plasters) with a big central marble table where the first registration of the incoming jobs is made.
In this section we have a vacuum mixer, 2 trimmers, a dry and a water one, a vibrator, a high precision scales (Kern), 3 SAM articulators to mount the models with sideburns (for the calibration we use the Adesso Split system, that lets us calibrate all the articulators in the same way, to make them interchangeable, and it also makes possible for us to provide the articulator calibration to our customers so they can check the job without shipping the articulator everytime), 3 complete working locations, a box with aspiration for the finishing, a casting machine, and an induction melting machine, 2 pre-warm ovens, an ultrasonic cleaner, 2 aspiring hoods, 2 sanders with 3 modules, a motor cleanser with aspirator.
2 full time employees are working in this section.
Every kind of plaster is mixed in vacuum mixers according to the producer's indications and calibrated with the right proportions water/plaster.
According to the plaster's or lavoration's type, we trim the model, with the dry trimmer if it's a precision model, or with the water one for all the others.
Model and antagonist are mounted on articulator, after this, the boxes with the models mounted on articulator with labsheets and the related documentations are sent to the next section.
Esthetic
It's the section where we finalise the jobs, from the single unit to the full arch restorations.
Receiving images from the dentist with the support of an Apple Pc which allows us to have an extremely precise observation of the morphologic and cromatic characteristics, shades and enamel trasparency, opacity and translucency of the tooth, dentine or enamel's crack line, superficial or internal colorations and the right collocation and width of the tooth which will permit us to reach a perfect esthetic integration of our prothesis with the rest of the mouth.
First of all we analise the job, after that, we bring it to the next step which is the building and layering of the different types of Noritake porcelain for Zirconia, Metal, Disilicate and Allumina, according to the different needs and requests of the dentist.
During the modelation phase we try to stick with the morphologic and functional characteristics of the natural teeth. Once finished with the layering and cooking of the porcelain, the prothesis will be finished and checked in the articulation and function, in the correct buccal-occlusal proportions, and to finish it, a superficial weaving is made to obtain a better esthetic integration.
In the construction of ceramic Veneers we can use different layering techniques that can be used to solve discoloration or teeth's fracture.
A technique consists on apply directly the ceramic on duplicates of the preparations in refractory material, thing that permits the maximum possible precision and a very good esthetic despite the reduced thickness.
Another technique is the construction of Disilicate veneers, and for this there are 2 different techniques as well:
The layered technique, where after the pressing of the material we proceed to the finish and consequently we're gonna add translucent ceramic masses with low melting point, after that we proceed with a new finishing and polishing, or, instead, proceeding directly with the shading and the polishing of the prothesis (Stain technique).
Our objective is to provide prothesis which will allow the dentist to an easy collocation with the least effort, facilitating the dentist in timing, and the best esthetic and comfort for the patient.
Dentures
In the denture's section we have 4 complete work locations, 2 SAM articulators, 5 handpieces, 2 curings, 2 boxes for finishing with aspirators, a lamp for curing, an oven and press to realise Nylon prothesis.
In order to realise custom trays or articulation bases we use curing base, adapting it on the model after a precise Wax-up, so we get to the light-curing step and subsequently finish them with a tungsten carbide burr; In the articulation's bases another wax is added.
The lavoration regarding dentures or partial prothesis and their finalisation, is made mounting the teeth with lines from the best available brands selecting them in function of their morphology and characterisation, a maniacal attention to the occlusion and firstly to the function.
The next execution of the flanges wax-up sees the pre-use of a wax, before sending the job to the surgery for the phonetic and articulation tests done by the dentist.
When the prothesis comes back from the tests, we apply changes to it, if needed, proceeding to the finishing and polishing steps.
Regarding the realisation of nylon prothesis which have their own strict protocol to follow, a particulare mitten is used during the finishing step.
In the same section are prokected the skeletonized dentures; through an analysis of the model executed with parallelometer, teeth equators are underlined and the undercuts are downloaded with wax, then duplicate the models with gel, in order to be developed with refractory material.
Subsequently we're going to shape the hooks and the plate with the preformed; finished this step, everything is brought to the fix prothesis section which will go on with the fusion and finishing steps.
Fixed Prothesis
In this section we count 5 complete work locations which occupy 3 full time workers, furnished with 3 stereomicroscopes, 2 Leica and a Zeiss, 3 SAM articulators, 4 handpieces, a parallelometer milling machine Shick, 3 electric tools, a water turbine, an oven specialised in carbon fiber cooking, an oven for metal's oxidation, an oven for the pressing of the ceramic, a laser welding (Dentaurum), a curing lamp, an Apple PC to analise the pictures received from the dentist.
In this section every model is checked with the microscope to verify the impression's quality; if it doesn't show any problem, we proceed with the stump scraping in order to underline the preparation's margin. We apply a layer of spacing varnish on the stumps, after thast we realize thermoformed copings, sealing (always under microscope) the margin with wax.
Once the margin is perfectly sealed with wax, we start the complete wax-up that will be reduced using a handpiece with calibrated burs, in order to get a frame which can be positioned on a cylinder base. On this base, we pour the coating plaster, proceeding with the metal fusion.
Once the fusion is done, we continue with another metal cooking in order to homogenizate it, so the frame goes for finishing and it's sent to the dentist for a try-in.
When it comes back from the try-in, approved by the dentist, we go on with the frame's preparation for the application of the ceramic. This preparation foresees the oxidation and the application of a matting mass. As underlined before, every step in this section is made using a stereomicroscope.
Many are the techniques adopted on bar's construction or implant's prothesis, for the realisation of these prothesis typologies we use a parallelometer milling machine to parallelize the mesostructures.
The lithium disilicate pressed crowns, after the complete design is done, are placed in a cylinder, clad with Press Vest, pressed in oven and, after a prothocol which foresees many treatments with sands and acids, is sent back to the esthetic section where it will be finished and polished.